Pad use scenarios.
Microfiber pads are commonly used primarily for cutting, and the reason is, microfiber not only can generate more heat than foam, it also holds heat. During cutting, not only the abrasives are at work, heat plays a significant role in paint levelling as well. Heat softens paint which allows the abrasives to cut into it easier, and not only that, it also helps paint 'move' and 'meld' into place. Have you seen self-healing PPF? When light scratches are introduced and heat is applied (doesn't need to be too hot, about ~60C), the film self-heals. This is also true to paint, the softer the substrate (paint) the more apparent the self-healing is, and this is crucial for cutting hard clearcoat. But the fibres do feel a little soft, right? Not when it starts spinning and ''whipping' on the paint.
Another contributing factor for the added cutting power is the thickness of the pad, normally microfiber pads are disc-like thin, which means less cushioning and results in better power transfer. But that also means these pads will have a harder time going over contours and concaves (can be remedied with an interface pad), and the user can experience more fatigue.
Microfiber pads are not as commonly used for finishing polish versus foam, because foam is ''flatter/smoother" than microfiber (during polishing, the fibres tend to bundle up), and the flatter the pad surface, the smoother the finish should be, theoretically at least. You still can get great results with a microfiber polishing/finishing pad such as Lake Country's OSP, Black Microfiber and Buff and Shine URO-Fibers, but we generally recommend foam for finishing softer paint (Japanese vehicles, for example).
Something to note about microfiber pads is that as the pad wears over time, the fibres will get shorter, resulting in an increased cut versus foam's decrease in cut (foam cells will soften and collapse over time).
Lake Country's Aggression Chart
The chart on the right is from Lake Country, but we like to share our own view on this. The microfiber cutting pad on the left of the chart states it cuts like a 10 (high cut) but can finish at an 8 (high gloss). The 10 cutting we have no problem backing, but having a finish of an 8 is debatable (on a new pad perhaps). As mentioned above, when a microfiber pad wears over time, the fibres will shorten, which means it gets more and more aggressive as it wears. So, after a few panels or projects, it may now have a cut of 11 and a finish of 5.
The One Step Pad (OSP) actually finishes surprisingly well even on softer paint (results also dictated by the accompanying polish/compound), it cuts and finishes well on both hard and soft paint.
Personally, we like to finish with foam, the Black Microfiber Pad though no slouch (it finishes equally well as foam does), we just prefer working with foam as generally, they're thicker and more comfortable to work with.
Bonus: the Black Microfiber Pad works really well with polishing metal, chrome and aluminium, it's like a microfiber towel that you can velcro onto a polisher, your arm will thank you.
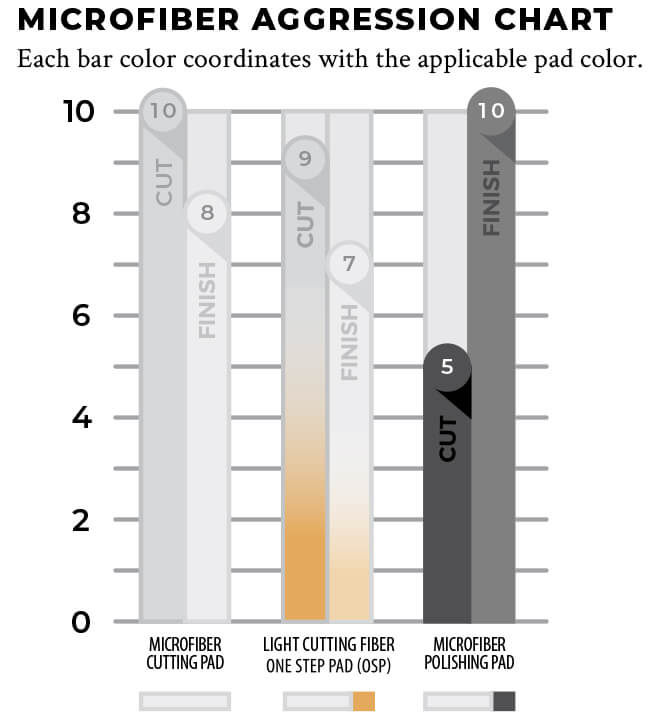
Cleaning and taking care of the pads.
As mentioned above, microfiber pads tend to generate and hold more heat, which can result in sooner glue/velcro delamination. Not only that, solvents from polishes & compounds can travel in quicker through the foam (because it's thinner) to soften the glue that holds the fibres to the foam to the velcro, and then the pad delaminates and "blows up". One way to remedy this is, to change out the pad more often, instead of doing 2~3 panels per pad, lower the coverage to 1~2 panels. Keep a bottle of water on the side and spray the pad to keep it slightly moist. And don't peel the pad off your backing plate while the pad is still warm and moist, use a pad removal tool instead to prevent delamination.
And remember to brush up the fibres after each section pass, the fibres tend to get fairly matted down and bundled up, you want to use a brush to loosen the fibres and get the compound debris out.
After you're done with your projects, the pads can simply be washed by hand in the sink or soaked in a bucket of detergent to soften compound residues.
Utilize an interface pad to add thickness for working on body lines, contours, and concaves.

The two bars on the left are the Microfiber Cutting and OSP pads, and the Blue Heavy Polishing, Orange Polishing and Black Finishing are Lake Country's SDO and HDO foams. And no, the colours are not in sync, orange doesn't mean it's the same orange across the board. For example, the Orange Lake Country Hybrid Force pad is a cutting pad, whereas SDO/HDO Oranges are for polishing.
More Quick Posts📖
Shinemate EX620 All you need to know.
Rupes Killer? Sort of. Not quite. Well, maybe. A forced-rotation-like DA polisher that hangs with the best at an entry-level price.
To Graphene or not to Graphene?
To Graphene or not to Graphene? We get asked this a lot. Graphene & Traditional Ceramic Coatings.